- HOME
- Wow! Cool Laboratory [Researcher Introduction]
- Munekazu Ohno
Wow! Cool Laboratory [Researcher Introduction]
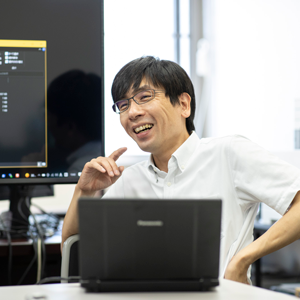
Division of Materials Science and Engineering,
Research Group of Materials Design,
Laboratory of Microstructure Control
Field of research: computational materials science
Research themes: mathematical modeling and computer simulation of microstructures in materials
E-mail: mohno[a]eng.hokudai.ac.jp
A new direction for materials science from data assimilation: A cross-scale approach
Accurate prediction of the growth process of the solidification microstructure in metallic materials
In April 2022, Professor Munekazu Ohno of the Laboratory of Microstructure Control received the 2022 Commendation for Science and Technology from the Minister of Education, Culture, Sports, Science and Technology (Research Category). The awarded research topic was “Modeling and computational study on prediction of microstructure in metals.” The joint research with Professor Tomohiro Takaki of Kyoto Institute of Technology and Professor Yasushi Shibuta of the University of Tokyo earned high evaluations.
The research field of Professor Ohno is computational materials science. He has been developing mathematical models and computer simulation techniques that will lead to the creation of the innovative materials that are required for modern society and to a new technology that affords reduced development time.
“We are developing a simulation technique to accurately predict how dendrites will solidify during casting (Fig. 1),” says Professor Ohno. “Depending on the crystal growth process, the physical properties of the material—hardness, electrical resistance, corrosion resistance—will vary. Therefore, more accurate predictions of the shape, size, and growth rate of dendrites that appear during the growth process would provide valuable data not only for the development of solidification science but also for the optimization of industrial manufacturing processes.”
Fig. 1: A simulation of dendrites growing upward in undercooled liquid Al alloy. The growth is very similar to that of snow crystals.
Large-scale MD simulation enables the observation of nucleation
The development of techniques for predicting the microstructures of metals has been hampered by limitations on the reachable scale of computational methods, deficiencies in mathematical models, and a lack of usable data on the physical properties of materials.
To solve these problems, Professor Ohno and his collaborators, in the joint research “Modeling and computational study on prediction of microstructure in metals,” took three approaches.
1) The development of large-scale simulation techniques for microstructures
2) The development of the phase-field (PF) model for very accurately predicting microstructures during solidification and grain growth in practical alloys
3) The establishment of a new technique for data science that combines the PF model with the molecular dynamics (MD) method at the same space-time scale to compute the physical properties of materials (Fig. 2)
“Atomistic simulations using the MD method can be used to investigate the nucleation of crystals during the solidification of metals,” says Professor Ohno. “However, it is difficult to address this nucleation quantitatively using the PF model, i.e., to perform simulations at the microstructural level. Therefore, in our joint research, we conducted a larger-scale MD simulation that allowed us to clarify, for the first time, that heterogeneity actually exists in the homogeneous nucleation process.”
Fig. 2: A new method for estimating physical properties was successfully developed by combining the molecular dynamics (MD) method, data science, and the phase-field (PF) model.
Application of data assimilation for weather forecasting to materials science
One factor leading to the high evaluation of Ohno and his joint research is the novelty of introducing data assimilation, which has been utilized in meteorology and oceanography, to the field of materials science.
“Data assimilation has often been used to improve the accuracy of computational methods that are based on experimental data, but we have developed a unique method in which the MD method and the PF model, which are two methods at different scales, are combined in the framework of data assimilation,” says Professor Ohno. “We have developed a method of estimating mesoscopic parameters by combining the MD method with the PF model. This is a new approach for combining microscopic and mesoscopic methods at the same scale, and we call it a cross-scale approach.” (Fig. 3)
Through these efforts, they have succeeded for the first time in the world in simulating microstructures 100 times larger than those for the conventional PF method and in conducting MD simulations of 10 billion atoms. This has dramatically increased the accuracy of microstructural predictions of the solidification and grain growth of practically used alloys.
“In light of the advantageous computational power, our simulations using a supercomputer have yielded findings that are 15 years more advanced than those obtained using lab-level servers. We believe that this substantial progress in computational technique can make a significant contribution to materials development in Japan. We plan to further explore the possibility of using our cross-scale approach at a unique scale where the reachable scales of micro and meso approaches or meso and macroscopic approaches overlap, by using the large-scale simulation technique of this joint research.”
Fig. 3
“In the case of joint research with companies, I try to find the optimal balance between computational cost and predictive accuracy in terms of the practical utility of the research achievements.”