- HOME
- Wow! Cool Laboratory [Researcher Introduction]
- Naoki Hiroyoshi
Wow! Cool Laboratory [Researcher Introduction]
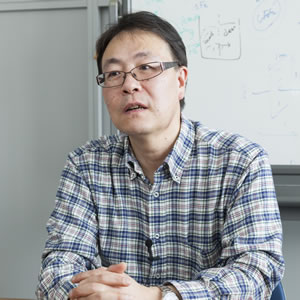
Division of Sustainable Resources Engineering,
Research Group of Resources Engineering,
Laboratory of Mineral Processing and Resources Recycling
Field of research: general engineering (earth/resource systems engineering), process engineering (processing properties, moving operation, unit operation)
Research themes: mineral processing engineering, resource recycling engineering, micromeritics, metal smelting engineering
E-mail: hiroyosi[a]eng.hokudai.ac.jp
Efficient separation and stabilization of harmful substances generated during mining to contribute to the production of high-quality mineral resources and environmental conservation
Prevention of environmental contamination by waste generated during resource mining
The Laboratory of Mineral Processing and Resource Recycling is the successor of a laboratory established at the Division of Mining Engineering when the School of Engineering was established at Hokkaido University and has mainly worked on the research and development of beneficiation techniques (techniques to separate and recover useful minerals from useless components) for minerals taken from mines. In the 1990s, when depletion of natural resources and material recycling became a social issue, “urban mines” attracted attention as centers for recycling unused resources accumulated in urban areas. Along with this trend, the research field of the laboratory has been expanded. In addition to beneficiation techniques for natural ores, the laboratory is now engaged in the development of recycling technologies for urban mines and waste.
As part of these studies, Professor Naoki Hiroyoshi develop new technologies to separate and refine natural mineral resources and prevent mine environment deterioration at the same time.
“For example, typical copper content in copper ore is less than 1%. More than 99% of material in the ore is unnecessary, so most of it is sorted out and left on site. Pyrite, a common mineral associated with copper ore and coal, is present in the waste, because its industrial value is extremely low. When pyrite is combusted with coal, sulfur portion in the mineral is emitted to air in the form of sulfur dioxide (SOx), a cause of acid rain. In addition, there are concerns that if it is left in a deposit site and weathered, the sulfur content will turn into sulfuric acid and contaminate the surrounding environment. As the demand for mineral resources increases around the world in the 21st century, the development of technologies to efficiently and sustainably use limited resources while minimizing the negative impacts on the environment is an increasingly important research challenge to be addressed.”
Professor Hiroyoshi and his research team are now working on a technology called Carrier Microencapsulation (CME) (note 1).
“This is derived from a serendipitous discovery. During our research on dissolving a mineral with acids, we found that the mineral did not dissolve at all when a certain type of organic matter was added. Further research revealed that the mineral was covered with a thin film of titanium oxide. Moreover, we found that organic component like catechol plays a role as carrier and a small amount of titanium in titanium mineral contained as an impurity was moved to form the film.”
High-quality coal efficiently refined using existing technology
Revolutionary CME, with which pyrite and other specific minerals are coated with a film, may simultaneously resolve two challenges in mining (i.e. the improvement of accuracy in sorting out valuable minerals from valueless minerals and the suppression of the weathering of pyrite, a cause of a mine environment deterioration). Professor Hiroyoshi and his team have developed a technology using CME for the separation and removal of pyrite associated with coal, and clarified the mechanism and benefits of the technology and optimum conditions for it through model experiments (note 2).
“The organic matter (carrier) necessary for CME is contained in coal itself, and it can be extracted from poor-quality coal in mines. Accordingly, it may be possible to make a closed system in which things available on site. CME uses conventional flotation technique for removing pyrite from coal and does not require new processing facilities. These things are the big merits of CME because refining resources into higher quality ones at a low cost provides a competitive advantage in mining industry.”
The use of materials available at a mine site for the efficient separation and removal of pyrite from coal and the prevention of the weathering of pyrite for stable storage significantly contribute both to the production of high-quality coal and the conservation of the mine environment. With increasing global demand for resources, the development of mineral resources has been expanding. Resource-rich countries overseas, however, are greatly concerned about environmental damage associated with resource development. If resource-rich countries request technological assistance to prevent environmental damage, this study could be offered by Japanese a competitive technology.
Hokkaido University and Kyushu University established the Collaborative Program for Resources Engineering, as a joint master’s degree program in April 2017. With the aim of effectively using limited mineral resources for a sustainable and advanced human society, this division intends to foster professionals with a global outlook and expertise on both science/technology and society/economy who can play key roles in securing resources in the future.
“Collaborative work with researchers from a variety of fields has increasingly been necessary in recent resources study. We expect new developments through the collaboration of multiple universities.”
Note 1. | Mechanism of Carrier Microencapsulation (CME) Pyrite is most often finely dispersed in the tissue of coal. In the traditional flotation method, there is a problem with crushed pyrite particles suspended in water because they attached to bubbles along with coal particles as a final product. In CME, however, only pyrite particles are coated with a thin film of hydrophilic silicon dioxide (SiO2) or titanium oxide (TiO2) in the pretreatment of flotation, which make it possible to separate pyrite and coal efficiently in flotation. This thin film also prevents the contact between pyrite, water and air when pyrite is discarded, thereby suppressing the generation of sulfuric acid associated with pyrite weathering. |
---|---|
Note 2. | Application of carrier-microencapsulation for coal flotation to remove pyrite and to suppress acid mine drainage formation at a tailing dam |
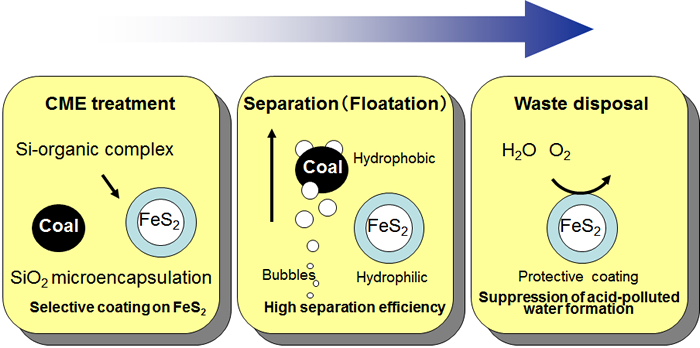
Figure 1. Outline of next-generation coal processing technology using CME
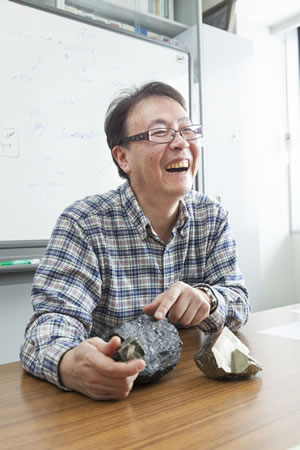
Coal and pyrite